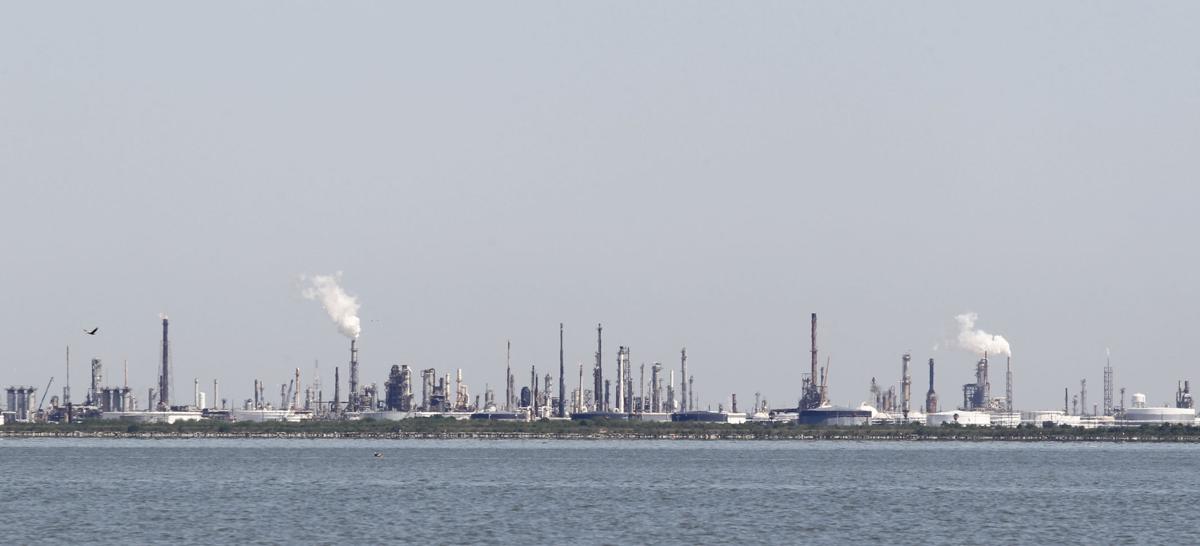
As industries around the country struggled to adapt during the onset of the coronavirus pandemic, one industry already was prepared.
The petrochemical industry has worked for years to reduce hazards in the workplace, and many companies already had plans in place for pandemics because of the global connectedness of the industry, said Lara Swett, vice president of technical and safety programs for American Fuel & Petrochemical Manufacturers, a trade association for the industry.
“This industry is very resilient,” she said. “They have a history of identifying hazards and mitigating hazards. So, adjusting in terms of protecting their employees, that’s just what they do.”
Adapting to the virus meant adopting practices that other industries also had to adopt, such as maintaining social distancing, wearing personal protective equipment and finding ways to identify infected employees.
But rather than draft new pandemic plans like many industries had to do, companies in the petrochemical industry simply had to pull out plans that already existed.
“For us, we actually had a pandemic plan for our site based on one of the SARS outbreaks,” said Michael Meyer, manager at Ashland Inc.’s chemical manufacturing plant, 4501 Attwater Ave. in Texas City.
But the severity and longevity of the pandemic forced the industry to reevaluate those plans, adapting them for what would turn out to be a much longer pandemic than expected.
“When we quickly got into COVID, it was probably a lot more severe and we realized we needed to dust our pandemic plan off,” Meyer said.
SAFETY MEASURES
Early on, employees in the petrochemical industry were recognized as essential workers. This meant they were exempt from orders to stay at home and many had to go in to work despite the virus. Although some employees were able to work from home, some functions of plant operation had to be done in person.
Across the industry, companies put in place distance guidelines and required employees to wear personal protective equipment, Swett said. But because plant employees already had to wear protective equipment, the added layer was not a big challenge, she said.
“They adapted very quickly and a lot of that had to do with that the industry has always been identifying hazards and mitigating against them,” she said.
Locally, Ashland created a series of four phases based on how the community was doing with COVID, Meyer said. In phase 4, the most restrictive, all employees had to wear KN95 masks, which meet strict standards, and stay 6 feet apart.
“We actually issued every employee their own keyboard and their own mouse early on in this thing so they could come in and not have to worry about their stuff being sanitized,” he said.
Employees who worked together also were grouped in their own break area to prevent people from mingling and spreading the virus, Meyer said.
“We kind of put different projects and contractors on their own island and didn’t let them interact with the rest of the plant,” he said.
Companies also saw an increased use in technology, Swett said. This meant using cell phones, drones and robots more frequently and adopting remote training, she said.
“People still need to get the adequate training they need,” she said.
MANUFACTURING GOALS
Some companies in the petrochemical industry also began manufacturing new products, Swett said. Many started making hand sanitizer as the demand for hand sanitizer rose, while others pivoted to making products that were used in N95 masks, she said.
“The industry has really been supportive of developing PPE for the health care industry and first responders,” she said.
It also was important to continue making the products that people needed.
Ashland, which manufactures polyvinylpyrrolidone, an inactive ingredient in medicine used as a binder for capsules and granules, among other things, felt the pressure to continue to meet the demand for its products, Meyer said.
“Definitely during this time, it’s important for us to make sure we’re able to supply because everyone around the world needs their medicine still,” he said.
And although the company was successful, the pandemic just added to an already complex process.
“It just added a whole other layer of complexity to everything that we do every day,” he said.
ADAPTING FOR THE FUTURE
It is too soon to tell how the pandemic will permanently change the petrochemical industry, Swett and Meyer agree. The increase in the delta variant sent some companies back to using protections they had discarded when the pandemic appeared to be lessening.
“I think that’s a hard question to ask right now because we had a point where some of the sites were limiting the restrictions they had during the summer and now a lot of those had to come back because of the delta variant,” Swett said.
Meyer is hopeful the industry will eventually return to normal. The situation is supposed to improve next year, but the future remains uncertain, he said.
“We don’t know if this is here to stay or something that’s going to clear up and allow us to go back to normal,” he said.
"industry" - Google News
October 23, 2021 at 10:45AM
https://ift.tt/2XEkx5d
Petrochemical industry, already prepared for pandemic, continues to adapt - Galveston County Daily News
"industry" - Google News
https://ift.tt/2RrQtUH
https://ift.tt/2zJ3SAW
Bagikan Berita Ini
0 Response to "Petrochemical industry, already prepared for pandemic, continues to adapt - Galveston County Daily News"
Post a Comment